BY MISTY MILIOTO
As the fast-fashion industry continually pumps out more and more clothing, a number of companies are stepping up to address the environmental challenges posed by discarded textiles. One such company, Stockholm-based Circulose (formerly known as Renewcell), was founded in 2012 by innovators from the KTH Royal Institute of Technology.
“Circulose’s uniqueness lies in its patented process that transforms 100 percent of textile waste into a dissolving pulp, which can replace high-impact raw materials like cotton and viscose,” says Dr.Anna Sammarco, senior director of global business development and strategy at Circulose.
“This closed- loop, chemical recycling process not only reduces textile waste but also minimizes the need for virgin resources, thereby decreasing the fashion industry’s environmental footprint.” Circulose does so by taking in cotton-rich textiles that can no longer be used (such as production waste). The company then shreds the textiles, removes any coloring and creates a slurry.
“Contaminants like polyester are taken out,” Sammarco says. “What remains is cellulose — a biodegradable organic polymer that cotton, trees, and most green plants on earth are made out of.”
This slurry is then dried out to produce sheets of pure Circulose (also the name of the product the company creates). These sheets are packed into bales and shipped off to be made back into virgin-quality textile fibers by producers. The chemical recycling process loop is closed once brands design and produce new clothes using fibers made from Circulose.
“The company has collaborated with major brands such as H&M, Levi’s, and Zara to incorporate its recycled material into various products,” Sammarco says. “These partnerships indicate a growing demand for sustainable materials in the fashion industry. While Circulose pulp is more expensive than virgin wood pulp, this cost has a minimal impact on the final price of the product.
“There is a significant price amplification throughout the supply chain that is typical for all next-gen materials development but not related to any additional cost in the process from fiber to product,” Sammarco says. “Working closely with the value chain is key to bringing the price down and [creating] circularity at scale.”
In order for more manufacturers to incorporate recycled materials into their production lines, Sammarco says it is essential to demonstrate that these materials are both economically viable and meet quality standards. “Building strong partnerships and ensuring a reliable supply chain are critical steps toward achieving this goal,” she adds. So far, Circulose is making important strides in this direction.
“We’re working with over 150 suppliers in the value chain and launched with over 30 global brands,” Sammarco says. “By recycling textiles, we can reduce waste, conserve resources, and mitigate the industry’s carbon footprint.” Yet another company that is making waves in recycling textiles is Münster, Germany-based Eeden. Founded in 2019 at the Textile and Fashion Institute in Mönchengladbach by a team of experts in economics, textile technology, chemistry, and engineering, the company grew from the key realization that less than 1 percent of old clothing is recycled into new garments.
“We wanted to understand why and quickly discovered a major gap,” says Julian Hertrampf, marketing and HR at Eeden. “Existing recycling methods either led to down-cycling or were not economically viable at scale. Instead of seeing this as a limitation, we recognized the untapped potential in developing a solution. We designed our own recycling process, specifically tailored to handle blended textiles like poly-cotton. This enables us to recover high-quality raw materials, creating a viable path toward full circularity in the textile industry.”
Eeden first recovers cellulose and polyester simultaneously and then separates the fibers. The cotton is broken down into cellulose, which is cleaned to remove any dyes and additives. It is then used to make Lyocell, Viscose, or Modal — soft, breathable, and biodegradable fibers. Meanwhile, the polyester is broken down into its basic building blocks (PET monomers) that can be used to make new polyester fibers or other PET-based products.
“Cotton, polyester, and their blends make up approximately 70% of all textile waste,” Hertrampf says. “Focusing on these materials allows for maximum impact in textile recycling. Other fiber types offer future potential for expansion.”
Currently, Eeden is raising a funding round to support its expansion and to build a demonstration facility to validate and scale its technology. At the same time, the company is working with diverse European and international partners and preparing to build its first industrial production facility.
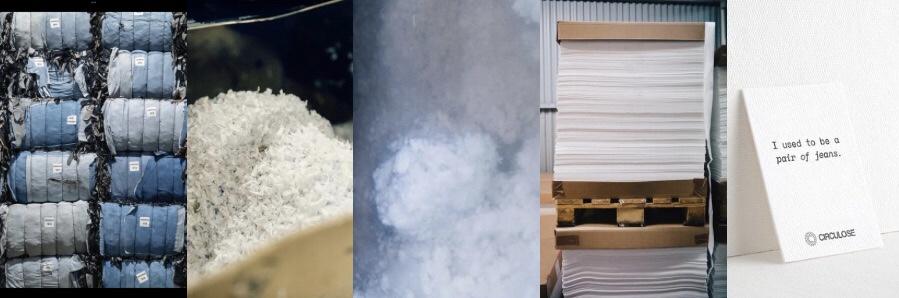
“Recycling textiles is not just about reducing waste,” Hertrampf says. “It also helps secure the future supply of raw materials. Extreme weather events like droughts and floods are making cotton harvests less predictable, creating challenges for the fashion industry. At the same time, as the global population grows, more farmland is needed for food instead of fiber production. Recycling is important, but it should be the last step in a truly circular system. The best approach is to use textiles for as long as possible — wear them longer, repair them when needed, and only recycle them when they are truly at the end of their life.”